Where Hydratight Can Help
For flange facing, pipe cutting, end prepping, milling, and much more – choose Hydratight to get it right first time, safe every time.
- We’ll come to you – no need for costly disassembly and transportation.
- Workshop tolerances achieved on-site.
- We’ll get your plant and equipment working again - quickly and safely.
- We own an extensive fleet of advanced machining tools – call us about any machining challenge!
- Solutions to suit you - new construction, modifications, planned shutdowns and emergency repairs.
- Call us about all sizes of project – we’ll help with the largest or smallest machining projects.
- Rapid Response
- Trusted and highly trained team - delivering decades of successful on-site machining results.
Hydratight On-Site Machining Services
The extensive Hydratight global fleet of machining equipment includes a huge range of specialist machines and accessories. For our customers, this means we can cater far beyond standard the standard in-situ machining applications offered by many other on-site machining companies.
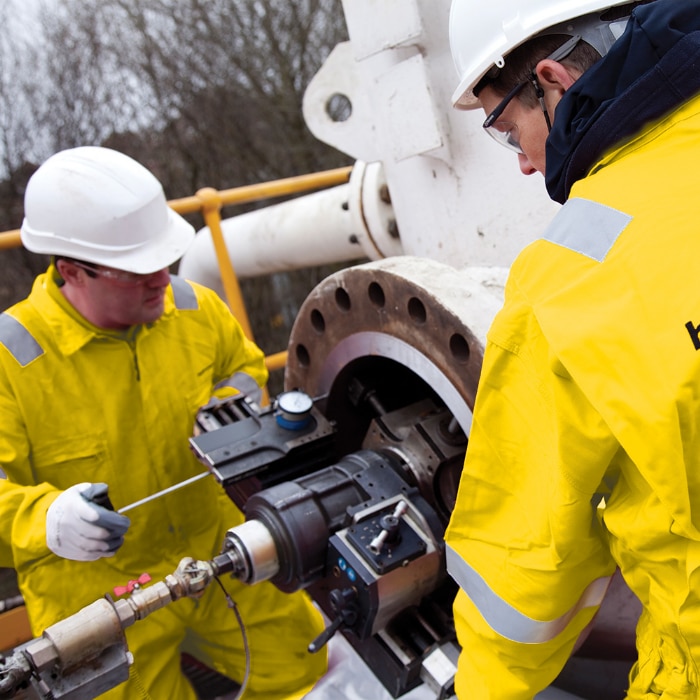
Flange Facing
What is Flange Facing?
During transit and installation, the faces of new flanges are easily damaged by either scratching or denting the sealing surface.
A flange surface may also be damaged by corrosion inside the joint through normal ongoing use.
Flange facing creates a new sealing surface, with either a spiral serrated finish or an RTJ groove (ring type joint).
In severe cases of corrosion, the whole flange will need to be removed using a clamshell pipe cutter.
Flange Facing Benefits
- Flange surfaces can be machined in-situ.
- Ensures the integrity of the flange joint.
- A new spiral grooved finish forces any potential leaked liquid to travel in a long spiral path, rather than across the flange face.
- Machining is carried out to ASME specifications.
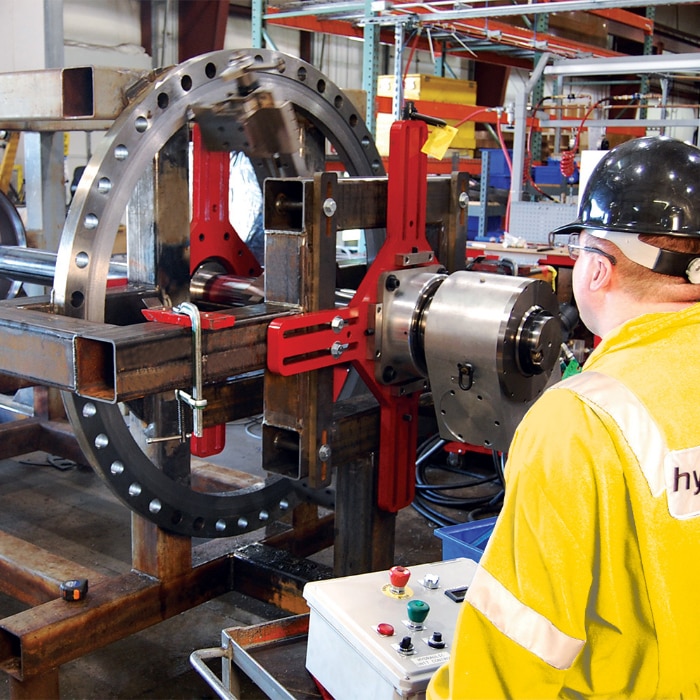
Line Boring
What is Line Boring?
When bores are not accurately aligned this can result in vibration, reduced efficiency, or even malfunction of the system.
Line boring is the re-machining of internal bores. Examples in the power generation industry include machining bearing housings, turbine casings, and other split casings.
Line Boring Benefits
- Performed on-site – reduces downtime and costs.
- Refurbished bores improve machinery efficiency.
- Material can be also added by bore welding and then machined back to original OEM dimensions.
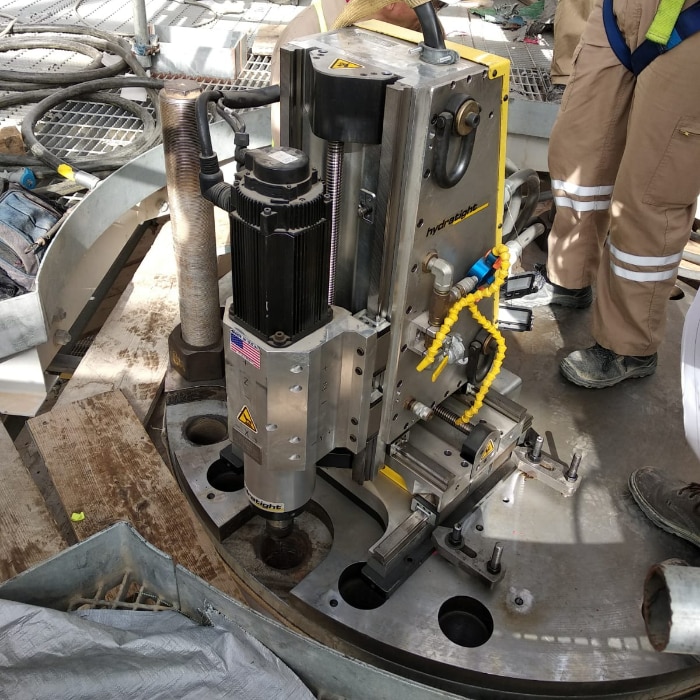
In Situ CNC Milling (geniSYS)
What is In-Situ CNC Milling?
In-situ CNC milling/machining uses the geniSYS machine which was developed in-house. It is used for removing cracked or broken studs up to 11" diameter and to accurately refurbish damaged threads.
Typical examples include manway covers and reactor studs.
In-Situ CNC Milling Benefits
- Accurate and repeatable machining of internal threads.
- A cold cutting operation.
- No need for manually controlled drilling or metal disintegration techniques.
- A single geniSYS machine is capable of both drilling and threading.
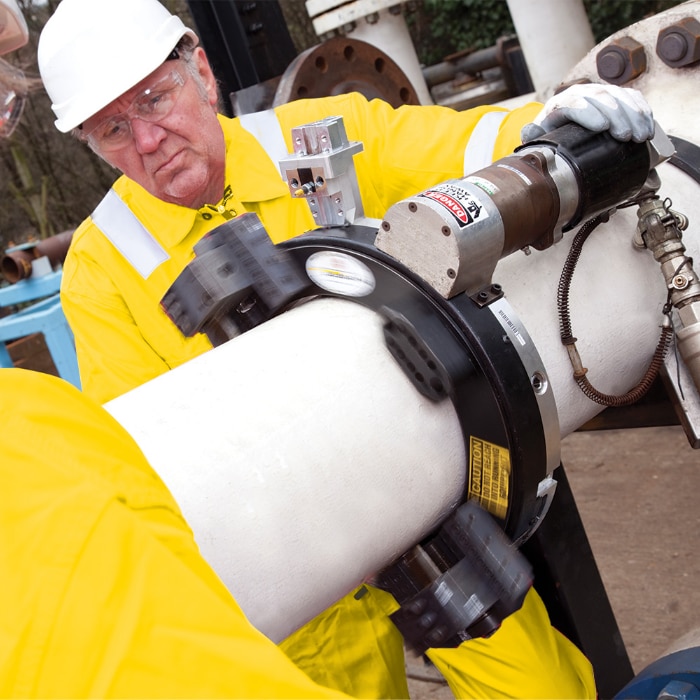
Pipe Cutting and Beveling
Pipe Cutting and Beveling is carried out using a clamshell cutter, (sometimes also known as portable split frame lathes).
Pipe Cutting and Beveling Benefits
- A cold cutting method.
- Large selection of machines available covering standard pipe diameters.
- Narrow body machines available to work in tight spaces.
- Heavy duty machines have the capacity to cut heavy wall pipes and large diameters.
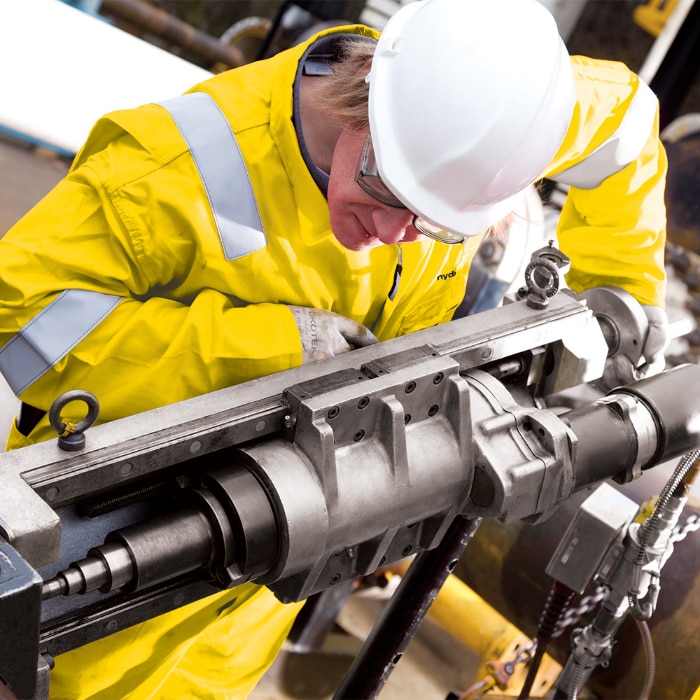
In-Situ Drilling and Tapping
This service provides multi-purpose drilling and stud removal onsite.
In addition to drilling, bores can be quickly rethreaded using our tapping machines.
Drilling and Tapping In-situ Benefits
- For all general purpose onsite tapping and flange stud tapping.
- Wide range of applications- our machines include a variety of mounting methods, including bolting, switch magnets, and chain clamps.
- Blind or through-hole tapping on a variety of sizes.
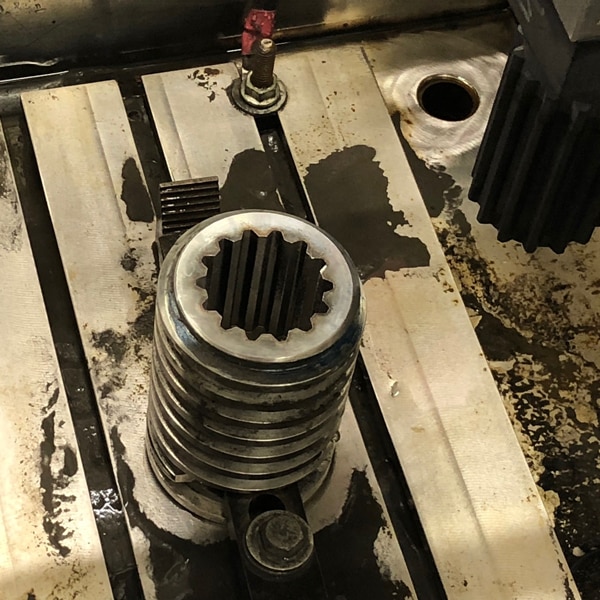
Electrical Discharge Machining
What is EDM (Electrical Discharge Machining)?
This is a process in which an electrode removes metal by reducing it into small particles.
The operation takes place submerged in a liquid such as oil or demineralized water. It is suited to projects where the high precision required is beyond what can be achieved with a machining tool.
Benefits of EDM
- Precise method of material removal.
- Clean method – ideal where there is a concern of foreign material entering the system.
- Suitable for a wide range of applications.
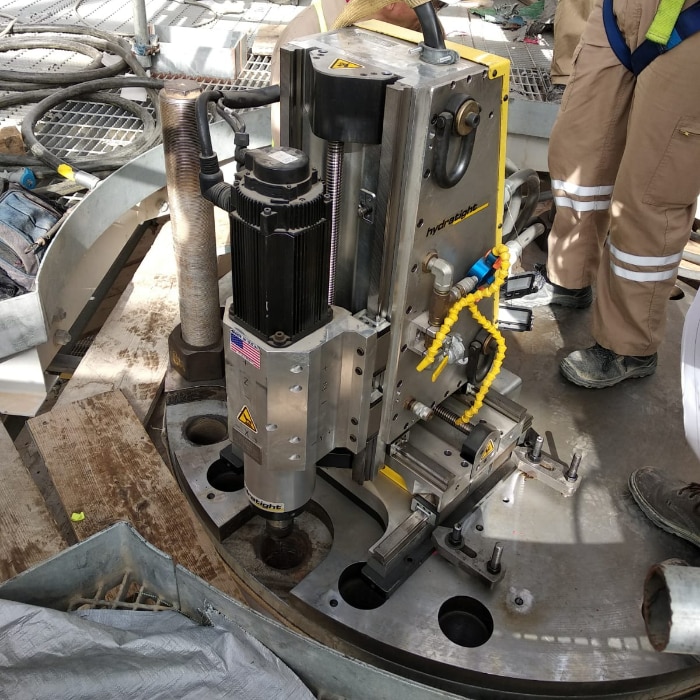
In-situ Surface Milling
What Is In-Situ Surface Milling?
Our in-situ milling service covers both 2-axis and 3-axis operations.
Example applications include:
- Mounting pads – where the mounting surface of motors and pumps is machined flat to prevent vibration.
- Heat exchanger refurbishment - machining division plate slots.
- Pipe seam weld removal - for an improved fit of pipe connectors.
- Turbine casing split lines.
Benefits Of In-Situ Surface Milling
- 2-axis and 3-axis milling operations.
- Heavy-duty and precise machining.
- Workshop precision delivered onsite.
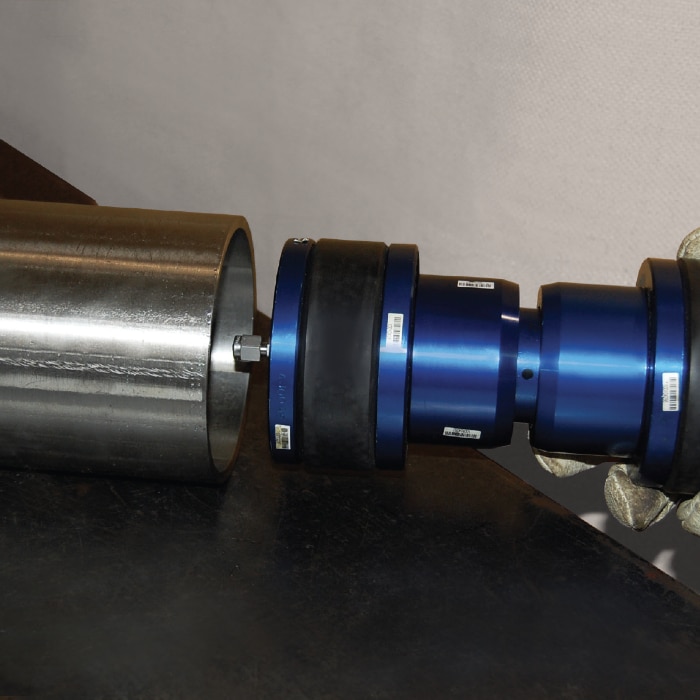
Heat Treatment
Heat Treatment In-Situ
Heat treating a metal can dramatically improve its physical properties and machinability.
Treatments involve the heating of metal alloys followed by cooling under controlled conditions.
Annealing
The metal is heated to a high temperature and slowly cooled to achieve the desired microstructure. This is usually to soften the metal.
Stress Relieving
involves heating to a high temperature -eliminating residual stresses.
Tempering
Heating the part after quenching - reduces brittleness, improves toughness.
Benefits of Heat Treatment
- Improve machinability.
- Increase hardness
- Improve consistency
- Soften
- Relive residual stress.
- Improve mechanical performance.
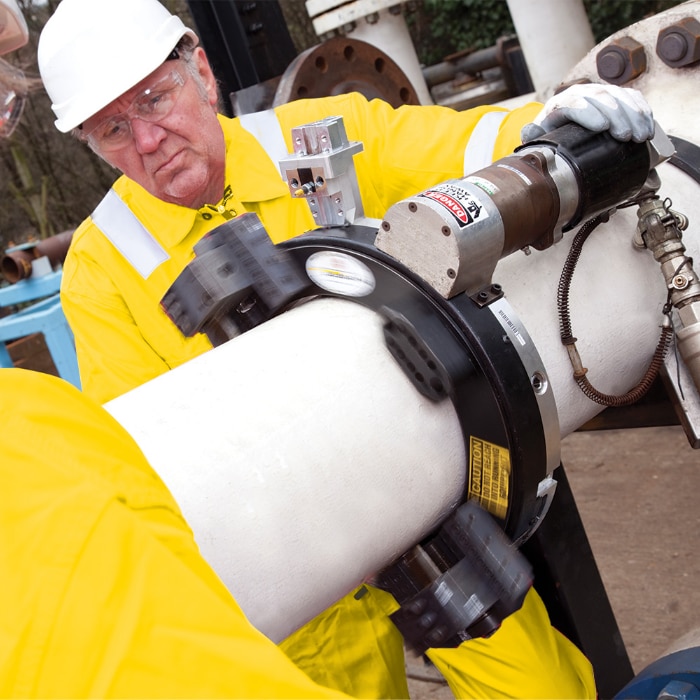
Metrology
In the oil & gas, power generation, and many other industries, critical components and assemblies need to meet strict tolerances.
Metrology is used to verify that these tolerances have been achieved.
Benefits of Metrology
- Hydratight technicians are highly skilled in using the latest measurement technologies - including Faro arms, and laser measuring equipment.
- All instruments are calibrated and maintained regularly.
Onsite Machining: Why Hydratight?
Successful on-site machining relies on the right people and the right equipment. Our people are qualified, competent and reliable - each working closely with our customers, ensuring they completely understand their requirements.
Our extensive fleet of advanced machining tools doesn’t just include the usual machining tools you would expect. Over the years we’ve developed advanced and customized products that are the envy of other on-site machining companies.
Testimonials
"The job was completed in a minimum time of 7 days working around the clock and in a professional manner "
- TSD Manager, Power Plant Department at Electric Company
"We strongly recommend Hydratight to all our projects and shutdown maintenance activities requiring bolting joints management and in-situ machining works. "
- Construction manager at General Industrial and Powergen Contractor
"We need to comment their good support to use especially for the flange re-facing jobs, and their quick response to meet all our urgent requirements."
- Project Manager at Oil & Global Energy Leader